宾夕法尼亚州立大学的研究人员开发了一种全新的多材料3D打印技术,成功地将两种不同的金属融合成一个复杂的结构。该团队采用一种名为多材料激光粉末床熔合的工艺,打印出了一种由低碳不锈钢和青铜组成的结构。这项成果得益于宾夕法尼亚州立大学的直接数字沉积创新材料处理中心(CIMP-3D),该中心于2023年8月购置了一套Aerosint选择性粉末沉积系统。
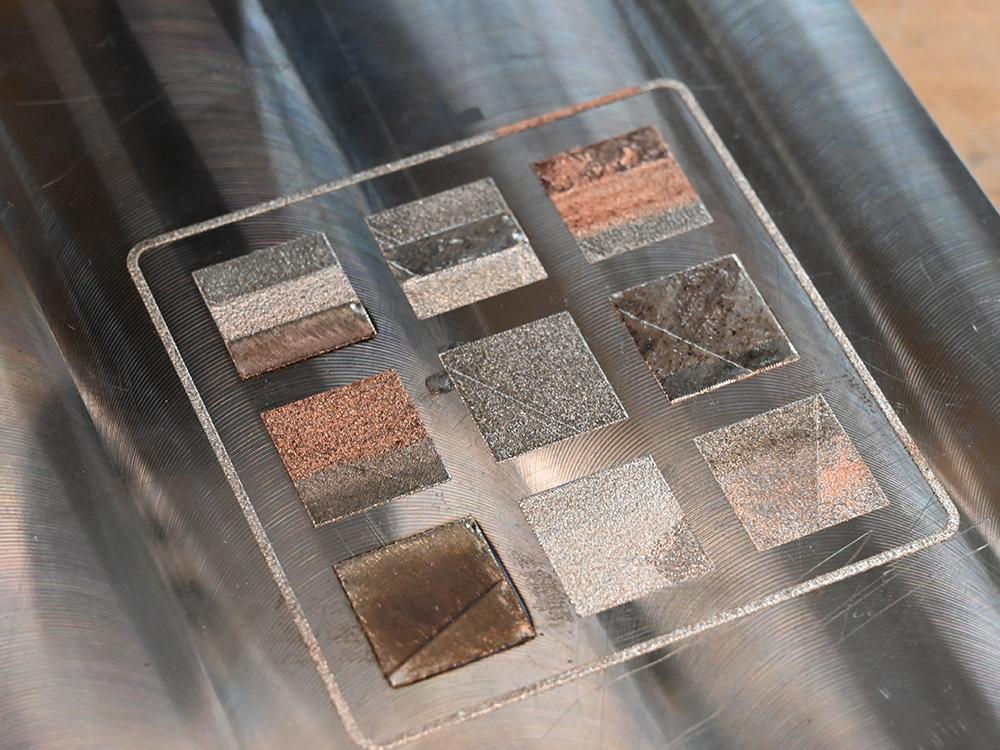
测试方块的打印平台特写图,其第一层烧结层由三种金属构成:不锈钢、因科镍合金和纯铜。测试方块展示了使用 CIMP-3D 新型选择性粉末沉积系统进行多材料金属增材制造的成果。(图片来源:SHAPE Lab、CIMP-3D 和 3D Systems。)
“在一种称为选择性粉末沉积的过程中,我们现在可以在增材制造过程中将多种粉末金属熔化在一层中——我们是美国第一所这样做的大学,”机械工程博士生、npj Advanced Manufacturing 上发表的论文第一作者 Jacklyn Griffis 说道。
研究人员专注于分析构建方向如何影响最终产品的质量。他们创建了一种称为螺旋状的复杂形状,可用于热交换器和生物医学植入物。该团队研究了开裂和孔隙等缺陷、界面微结构以及界面上的元素扩散,以了解这些因素如何影响性能。
“宾夕法尼亚州立大学一直是金属增材制造领域的领导者,但现在我们有能力制造复杂的多材料零件,我们不仅可以进行复杂的设计,还可以精确控制每种材料的放置位置,”机械工程副教授兼 CIMP-3D 联合主任 Guha Manogharan 解释道。
研究团队利用CT扫描生成零件的数字3D渲染图,从而识别孔隙和微米级缺陷等潜在问题。此功能可实时监控制造过程。据格里菲斯介绍,一个一厘米高的金属零件包含数千层金属粉末,需要数小时才能打印完成。
未来的工作将侧重于通过过程监控,将这种3D打印方法转变为更稳健、更易于生产的工艺。该团队还计划加入其他金属合金,例如因科镍合金和铜。该研究得到了应用研究实验室沃克研究生助教奖学金和美国国家科学基金会的支持。
资料来源:psu.edu