东北大学研究人员日本开发了一种多材料3D打印新方法,可以生产轻质且耐用的汽车零部件。该工艺结合了钢和铝等不同金属,并利用增材制造的精度来制造复杂且优化的组件。
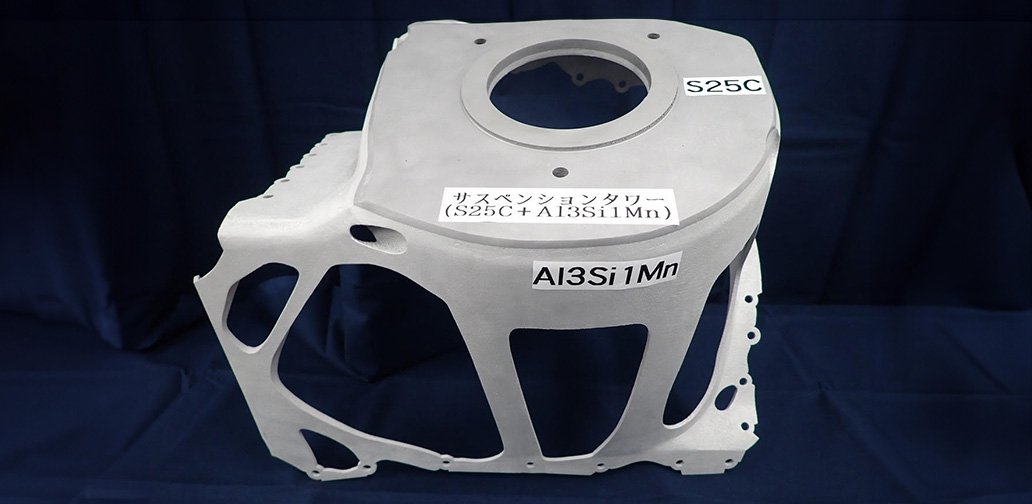
在金属印刷中,利用热量将材料逐层粘合在一起。与传统制造工艺相比,该技术不仅可以生产单独的几何形状,而且还可以减少材料浪费。多材料结构开辟了更多的可能性,因为它们专门结合不同的材料来提高组件的性能。然而,这种方法的一个主要问题是在异种金属之间的界面处形成脆性金属间化合物,这会影响机械性能。
为了解决这个问题,研究人员使用了激光粉床熔融(L-PBF)技术,其中使用激光选择性地熔化金属粉末。
“由于其工艺灵活性,多材料成为增材制造领域的热门话题,”副教授 Kenta Yamanaka(东北大学)解释道。 “然而,实际实施中的一个主要挑战是,对于某些金属组合,例如钢和铝,可能会在不同金属的界面处形成脆性金属间化合物。这使得材料更轻,但也更脆。”
这项工作的成果是一个功能齐全的汽车部件原型,即所谓的支柱支撑,具有定制的几何形状。
东北大学特聘助理教授 Seungkyun Yim 表示:“换句话说,你不能只是将两种金属放在一起,然后期望它们在没有计划的情况下粘在一起。”原地。”
研究人员计划将他们的发现应用于其他金属组合,以进一步扩大多材料 3D 打印的可能性。这些发展可以在各个行业中实现新的应用,特别是在重量和强度至关重要的行业。
【特别声明】本站部分内容来源于互联网,仅供个人用于学习、研究,不得用于商业用途。如有关于文章内容、版权或其它问题请及时联系我们修正或删除(微信:18923725282 / 邮箱:454884888@qq.com)。